General parts machining is a cornerstone of modern manufacturing, playing a pivotal role in shaping industries such as automotive, aerospace, and healthcare. This process involves the precise removal of material from a workpiece to create components with exact specifications. Whether it’s crafting intricate gears for a car engine or producing durable medical implants, machining ensures that parts meet stringent quality standards. The versatility of general parts machining lies in its ability to adapt to a wide range of materials, from metals to plastics, making it indispensable in today’s industrial landscape.
At its core, machining is about precision, efficiency, and innovation. Over the years, advancements in technology have revolutionized how machining is performed, introducing computer numerical control (CNC) systems and automation that enhance accuracy and productivity. These innovations have not only streamlined production but also opened new possibilities for customization and scalability. As industries continue to evolve, the demand for high-quality, machined parts remains constant, underscoring the importance of understanding this process in depth.
Despite its complexity, general parts machining is not reserved for experts alone. With the right knowledge and tools, anyone can gain insight into how machining works and its impact on the products we use daily. From small workshops to large-scale manufacturing facilities, this process is integral to producing components that drive innovation. Whether you’re a seasoned professional or a curious beginner, exploring the world of general parts machining offers valuable insights into the backbone of modern manufacturing.
Read also:Exploring The Life And Influence Of Candace Owens Family A Comprehensive Look
Table of Contents
- What Is General Parts Machining and Why Is It Important?
- Key Techniques in General Parts Machining
- How Does CNC Machining Transform the Manufacturing Process?
- What Are the Common Materials Used in Machining?
- Applications of General Parts Machining in Various Industries
- Challenges and Solutions in General Parts Machining
- Is Automation the Future of Machining?
- Frequently Asked Questions About General Parts Machining
What Is General Parts Machining and Why Is It Important?
General parts machining refers to the process of shaping raw materials into precise components through the controlled removal of material. This process is essential for creating parts that meet exact specifications, ensuring functionality, durability, and compatibility with other components. Machining is used across industries to produce everything from simple screws to complex aerospace components, making it a foundational element of modern manufacturing.
The importance of machining cannot be overstated. It enables the production of high-precision parts that are critical for the performance of machinery and equipment. For example, in the automotive industry, machined parts like engine blocks and transmission components must meet strict tolerances to ensure optimal performance and safety. Similarly, in the medical field, precision machining is vital for creating implants and surgical instruments that meet stringent regulatory standards.
Moreover, machining plays a key role in driving innovation. As industries demand more complex and customized parts, machining techniques have evolved to meet these needs. This adaptability ensures that machining remains relevant in an era of rapid technological advancement. By understanding the basics of general parts machining, businesses and individuals can better appreciate its impact on product development and quality assurance.
Key Techniques in General Parts Machining
There are several techniques used in general parts machining, each suited to specific applications and materials. These techniques form the backbone of machining operations, ensuring that parts are produced with the desired accuracy and finish.
Turning
Turning is one of the most common machining techniques, involving the rotation of a workpiece while a cutting tool removes material to create cylindrical shapes. This method is ideal for producing components like shafts, bolts, and bushings. Turning can be performed on lathes, which are available in manual and CNC variants, offering flexibility in production.
Milling
Milling involves the use of a rotating cutting tool to remove material from a stationary workpiece. This technique is highly versatile, allowing for the creation of complex shapes and features such as slots, holes, and contours. Milling machines come in various configurations, including vertical and horizontal setups, to accommodate different machining requirements.
Read also:Stephen A Smith Net Worth 1 Billion A Deep Dive Into His Success Story
Drilling
Drilling is a straightforward yet essential machining process used to create holes in a workpiece. It is often combined with other techniques like milling and turning to achieve the desired geometry. Drilling can be performed using manual drills or automated CNC machines, depending on the complexity of the task.
Grinding
Grinding is a finishing process that uses an abrasive wheel to remove small amounts of material, resulting in a smooth surface finish. This technique is commonly used for parts that require tight tolerances and high-quality finishes, such as bearings and gears.
EDM (Electrical Discharge Machining)
EDM is a non-traditional machining technique that uses electrical discharges to remove material. It is particularly useful for machining hard materials or creating intricate shapes that are difficult to achieve with conventional methods. EDM is widely used in the aerospace and medical industries.
How Does CNC Machining Transform the Manufacturing Process?
CNC machining has revolutionized the way parts are manufactured, offering unparalleled precision, efficiency, and flexibility. Unlike manual machining, CNC systems use computer programs to control the movement of tools and machinery, ensuring consistent results with minimal human intervention.
One of the key advantages of CNC machining is its ability to produce complex geometries with high accuracy. This is particularly beneficial for industries like aerospace and automotive, where parts often require intricate designs and tight tolerances. CNC machines can also operate continuously, reducing production time and increasing output.
Another significant benefit of CNC machining is its adaptability. By simply updating the program, manufacturers can switch between different parts or materials, making it ideal for small-batch and custom production. This flexibility has made CNC machining a cornerstone of modern manufacturing, enabling businesses to respond quickly to market demands.
What Are the Common Materials Used in Machining?
General parts machining can be performed on a wide range of materials, each offering unique properties that make it suitable for specific applications. Understanding these materials is essential for selecting the right one for a given project.
Metal Alloys
Metal alloys, such as steel, aluminum, and titanium, are among the most commonly machined materials. These materials are valued for their strength, durability, and resistance to wear and corrosion. Steel is often used in automotive and construction applications, while aluminum is favored for its lightweight properties in aerospace and consumer electronics.
Plastics
Plastics, including ABS, polycarbonate, and nylon, are widely used in machining for their versatility and cost-effectiveness. These materials are ideal for producing prototypes, enclosures, and components that require electrical insulation. Plastics are also lightweight, making them suitable for applications where weight reduction is critical.
Ceramics
Ceramics are used in machining for their hardness and resistance to high temperatures. These materials are often employed in applications like cutting tools and aerospace components, where performance under extreme conditions is essential.
Composites
Composites, such as carbon fiber and fiberglass, are increasingly used in machining due to their high strength-to-weight ratio. These materials are commonly found in aerospace, automotive, and sports equipment, where lightweight and durable components are required.
Wood and Foam
While less common, wood and foam are occasionally used in machining for prototyping and model-making. These materials are easy to machine and provide a cost-effective solution for creating mock-ups and visual aids.
Applications of General Parts Machining in Various Industries
General parts machining finds applications in a wide range of industries, each with its unique requirements and challenges. By understanding these applications, we can better appreciate the versatility and importance of machining in modern manufacturing.
Automotive Industry
In the automotive industry, machining is used to produce engine components, transmission parts, and suspension systems. These parts must meet strict tolerances to ensure optimal performance and safety. Machining also enables the production of lightweight materials, contributing to fuel efficiency and reduced emissions.
Aerospace Industry
The aerospace industry relies heavily on machining to create components that can withstand extreme conditions. Parts like turbine blades, airframe components, and fasteners require high precision and durability. Machining techniques like CNC and EDM are often used to achieve the required specifications.
Medical Industry
In the medical field, machining is essential for producing implants, surgical instruments, and diagnostic equipment. These parts must meet stringent regulatory standards and often require biocompatible materials. Precision machining ensures that these components are safe and effective for use in medical procedures.
Consumer Electronics
Consumer electronics rely on machining to produce components like housings, connectors, and heat sinks. These parts must be lightweight, durable, and aesthetically pleasing. Machining techniques like CNC milling and turning are commonly used to achieve the desired results.
Energy Sector
In the energy sector, machining is used to produce components for power generation and distribution. Parts like turbine blades, valves, and pumps require high precision and resistance to wear and corrosion. Machining ensures that these components can operate reliably under demanding conditions.
Challenges and Solutions in General Parts Machining
While general parts machining offers numerous benefits, it also presents several challenges that must be addressed to ensure success. By understanding these challenges, manufacturers can implement effective solutions to overcome them.
Material Selection
Selecting the right material for a given application can be challenging, as it requires balancing factors like cost, performance, and machinability. To address this, manufacturers often conduct material testing and consult with experts to identify the best options for their needs.
Tool Wear and Maintenance
Tool wear is a common issue in machining, leading to reduced accuracy and increased downtime. Regular maintenance and the use of advanced tool coatings can help mitigate this problem, ensuring consistent performance and extending tool life.
Surface Finish and Tolerances
Achieving the desired surface finish and tolerances can be difficult, especially for complex parts. Advanced machining techniques like grinding and EDM can help meet these requirements, while post-processing methods like polishing can further enhance the finish.
Cost Management
Managing costs is a critical challenge in machining, as it involves balancing factors like material costs, labor, and equipment. Implementing lean manufacturing practices and investing in automation can help reduce costs while maintaining quality.
Environmental Impact
Machining can have a significant environmental impact due to material waste and energy consumption. To address this, manufacturers are adopting sustainable practices like recycling scrap materials and using energy-efficient machinery.
Is Automation the Future of Machining?
Automation is increasingly becoming a driving force in the machining industry, offering numerous benefits that enhance efficiency, accuracy, and scalability. As technology continues to evolve, the role of automation in machining is expected to grow, shaping the future of manufacturing.
One of the key advantages of automation is its ability to reduce human error and improve consistency. Automated systems can operate continuously, ensuring that parts are produced with minimal variation. This is particularly beneficial for high-volume production, where consistency is critical.
Automation also enables greater flexibility in production. By integrating robotics and AI, manufacturers can quickly adapt to changing demands and produce a wide range of parts with minimal setup time. This adaptability is essential in an era of rapid technological advancement, where businesses must respond quickly to market trends.
Despite its benefits, automation also presents challenges, such as high initial costs and the need for skilled operators. However, these challenges can be overcome with proper planning and investment in training. As automation continues to evolve, it is likely to become an integral part of general parts machining, driving innovation and efficiency in the manufacturing process.
Frequently Asked Questions About General Parts Machining
What is the difference between CNC machining and manual machining?
CNC machining uses computer programs to control tools and machinery, ensuring high precision and consistency. Manual machining, on the other hand, relies on human operators to control the tools, making it less precise but more flexible for small-scale projects

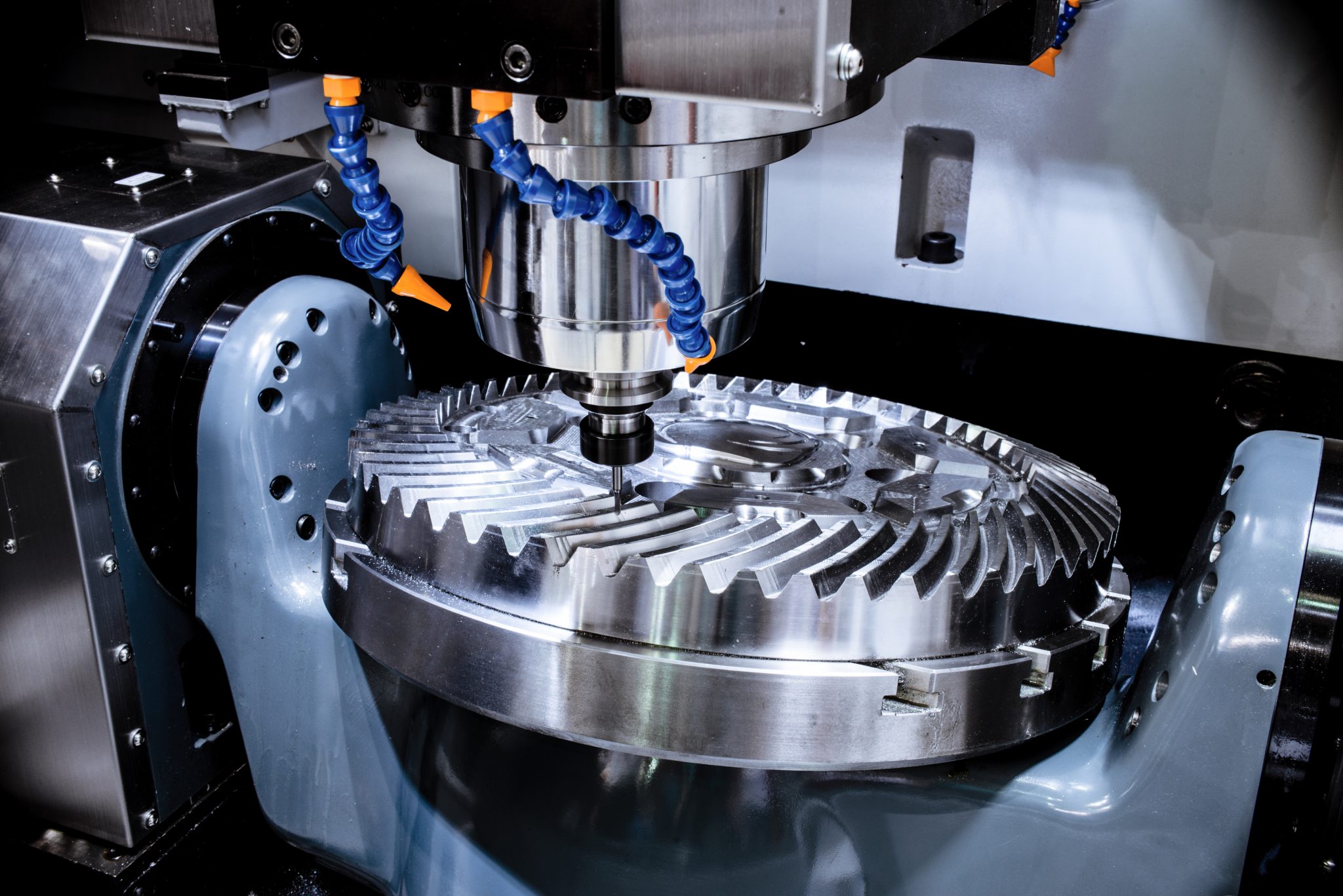